Injection mould
Injection moulding can’t be done without an injection mould. A mould has a cavity that is the reverse, the negative, of the final product. In order to create a plastic product, an individual injection mould is required for each product or component. Different types of plastic can be injected into a mould at high temperature by an injection moulding machine. This plastic then cools off in the cold injection mould, becoming a dimensionally stable product. The mould ensures that a product takes on a characteristic shape or that a product part fits seamlessly in the assembly stage.
The product is ejected from the machine within 15 to 60 seconds, depending on the wall thickness, and cools down further. Each injection is referred to as one injection cycle. An injection mould can be single or multiple; the decision is mainly dependent on the annual volume and the investment in the mould. A single mould has just one mould, while a multiple mould has several moulds in one injection mould. The number of cavities (voids) in one injection mould is known as the mould’s multiplicity.
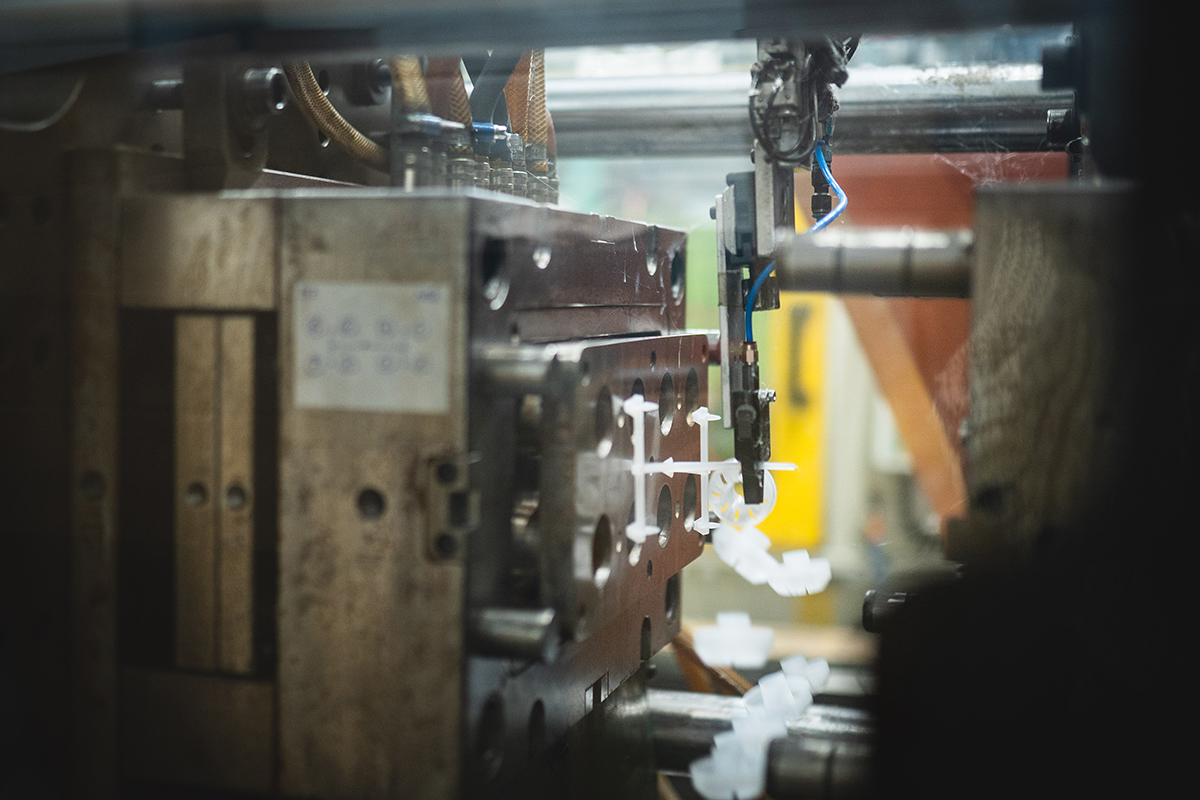