ABS injection moulding
ABS is an amorphous plastic and is a styrene polymer. ABS consists of Acrylonitrile Butadiene Styrene; it can easily be processed in our injection moulding machines. ABS is suited to many different applications, making it a widely used plastic in various end products. ABS is popular because this polymer is light, hard, and impact-resistant. It has high stiffness and can easily be finished with a very high boundary surface. A disadvantage of ABS is that it is sensitive to weather conditions and UV light.
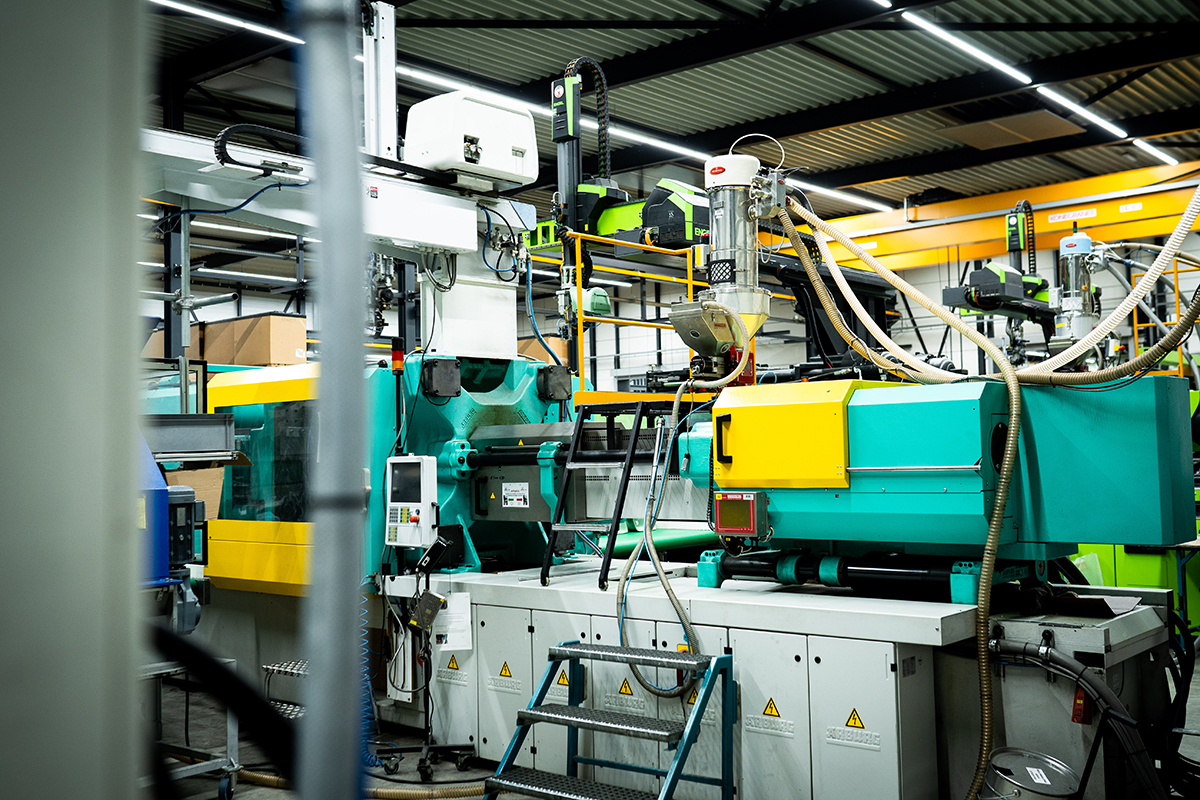