Types of plastics
Thermoplastics are widely used in the injection moulding plant. We’re familiar with a range of thermoplastics, each with different properties. PVC, PMMA, PVAC, PS and PC are amorphous plastics. With the exception of PC, these plastics are usually hard and brittle. Crystalline plastics mostly have an ordered structure. This group includes PE, PP, PVDF and PTFE. Would you like to know more about the thermoplastics that we at Wicro often work with? Take a look at types of plastic.
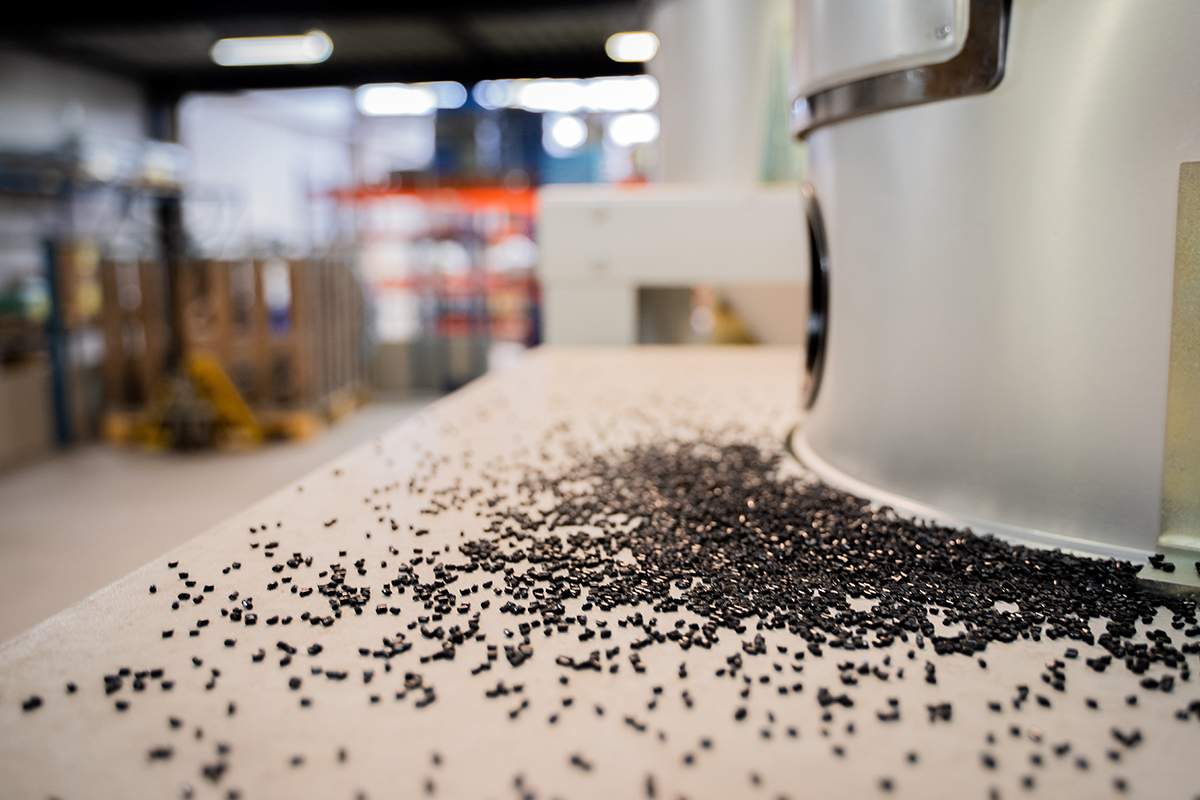