Lightning-fast onboarding and project management
Maxado’s onboarding is the perfect example of efficient project management. We went from quote to production within four weeks. This was quite a challenge, involving hundreds of different steps. We went through these one by one with the Stage-Gate Model and we even installed an 1150-tonne injection moulding machine in a short period of time. Nothing escapes our attention and we don’t miss a single detail. Thanks to our close collaboration and a dedicated project manager, Maxado didn’t lose any valuable time.
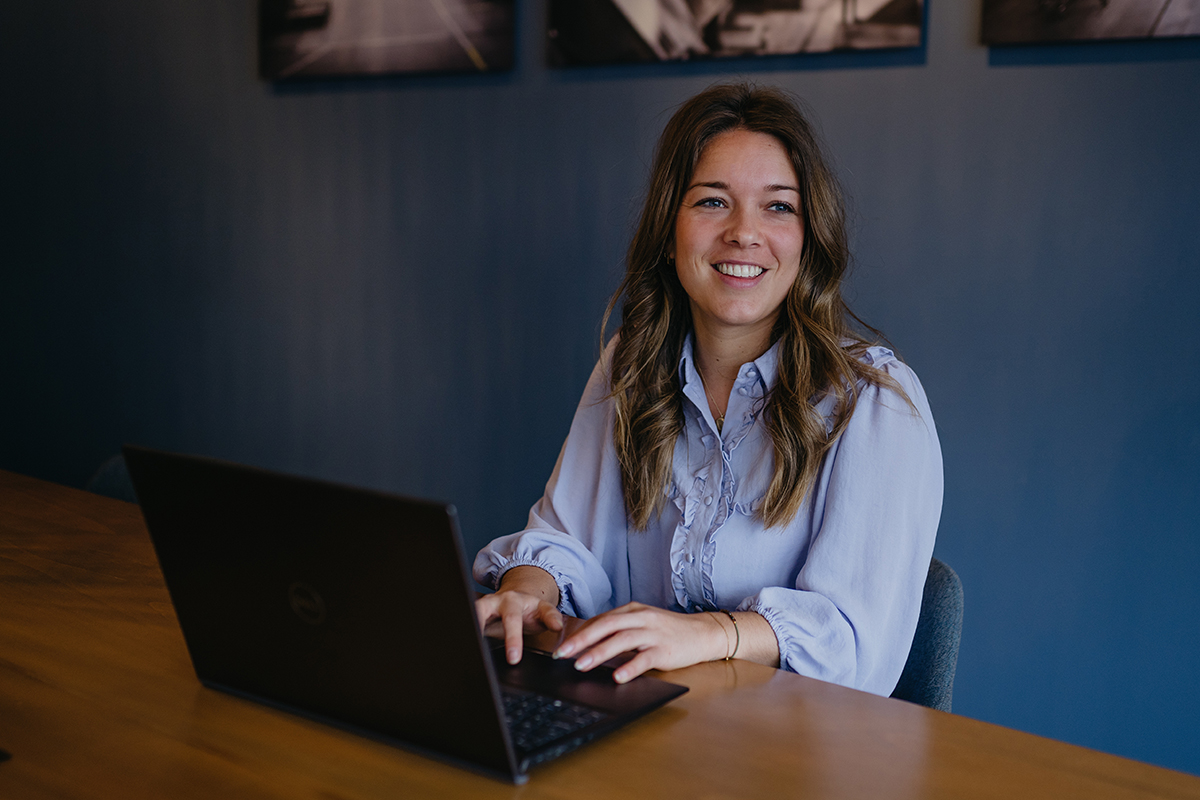